What is LiDAR?
LiDAR, also known as optical radar, is the abbreviation of Light Detection And Ranging system. It is a system that emits laser beams to detect characteristics such as the position and speed of the target. Its working principle is to send a detection signal (laser beam) to the target, and then compare the received signal (target echo) reflected from the target with the transmitted signal, and after proper processing, the relevant information of the target can be obtained, such as Parameters such as target distance, azimuth, altitude, speed, attitude, and even shape, so as to detect, track and identify targets.
Check out our range of lidar products.
Since the invention of LiDAR in the 1960s, LiDAR has developed on a large scale. At present, LiDAR manufacturers mainly use laser transmitters with wavelengths of 905nm and 1550nm. Light with a wavelength of 1550nm is not easy to transmit in the liquid of the human eye, which means that the power of a laser radar with a wavelength of 1550nm can be quite high without cause retinal damage. Higher power means longer detection distance, and longer wavelength means that it is easier to penetrate dust haze. However, due to cost reasons, the production of LiDAR with a wavelength of 1550 nm requires the use of expensive gallium arsenide materials. Manufacturers choose to use silicon materials to manufacture 905nm lidars that are close to the wavelength of visible light, and strictly limit the power of the transmitter to avoid permanent damage to the eyes.
Different Working Principles of LiDAR?
Time of Flight
The principle of ranging is currently mainly based on the time of flight (time of flight) method, which uses the time interval between the pulse signal emitted by the transmitter and the reflected pulse signal received by the receiver to calculate the distance to the target object. Please find the indication of Time of Flight principle for details.
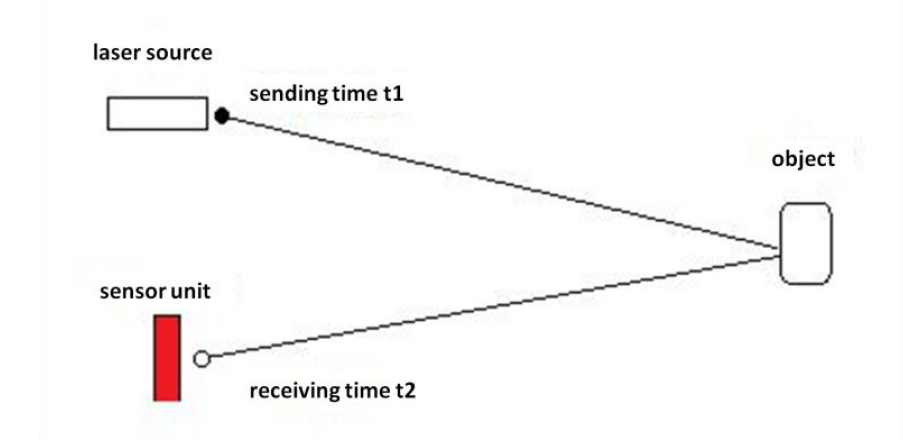
Distance = Speed of Light*(t2 – t1)/2
Time of Flight LiDAR is mainly used for perception unit for autonomous driving, robotics, V2X and surveying application. Learn more details >>.
FMCW - Frequency Modulated Continuous Wave
There is also a coherent approach, where a frequency modulated continuous wave (FMCW) lidar emits a continuous beam of light with a frequency that varies steadily over time. Since the frequency of the source beam is constantly changing, the difference in beam transmission distance will lead to a difference in frequency. After mixing the echo signal with the local oscillator signal and low-pass filtering, the difference frequency signal obtained is a function of the round-trip time of the beam. Frequency modulated continuous wave lidar will not be interfered by other lidars or sunlight and has no ranging blind zone; it can also use Doppler frequency shift (Learn more about How Doppler LiDARs Work) to measure the speed and distance of objects. The concept of frequency-modulated continuation wave LiDAR is not new, but it faces many technical challenges, such as the limit of the line width of the emitted laser, the frequency range of the chirp, the linearity of the change of the chirp frequency, and the reproducibility of a single chirp Wait.
AMCW - Amplitude-Modulated Continuous-Wave
Amplitude-modulated continuous-wave (AMCW) lidars are similar to basic time-of-flight systems in that AMCW lidars emit a signal and measure the time it takes for the laser light to reflect back. But the difference is that time-of-flight systems emit only one pulse, while AM CW LiDAR achieves modulation by changing the pole current in the laser diode to adjust the intensity of the emitted light.
Different Structure Types of LiDAR?
LiDAR mainly includes laser transmitter, receiver, scanner, lens antenna and signal processing circuit. There are two main types of laser emitting parts, one is laser diodes, which usually have two substrate materials, silicon and gallium arsenide, and the other is the very hot vertical cavity surface emission (VCSEL) (such as LiDAR on the iPhone), VCSEL The advantages are low price, very small size, and extremely low power consumption. The disadvantage is that the effective distance is relatively short, and multi-stage amplification is required to achieve the effective distance for vehicles.
Lidar mainly applies the principle of laser ranging, and how to make a suitable structure so that the sensor can emit laser beams in multiple directions, and how to measure the time for the laser to go back and forth, which distinguishes different lidar structures.
Mechanical LiDAR
Take Leishen’s C16 lidar, which stacks 16 lasers vertically so that the entire unit rotates many times per second. There is a physical rotation between the transmitting system and the receiving system, that is, by continuously rotating the transmitter, the laser point becomes a line, and the multi-beam laser transmitter is arranged in the vertical direction to form a surface to achieve 3D scanning and receiving information.
Leishen C16 applies innovative structure to integrated the transmitter and receiver on the 2 piece of PCB, which increased the stability and quanlity of LiDAR significantly.
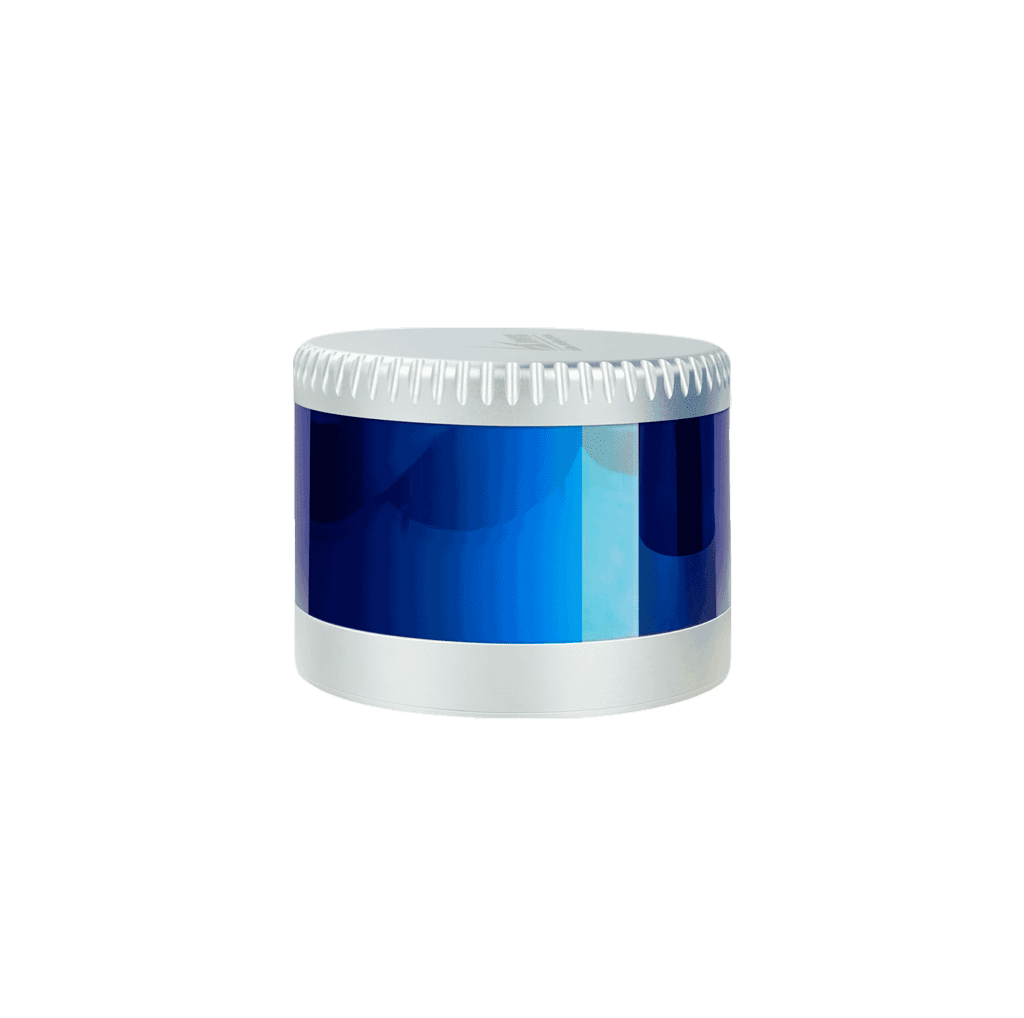
- Using leading core signal processing ASIC chip and advanced multiple echo detection technology, data calibration technology
- Acquire data up to 64/320,000 points per second, accurately, quickly and clearly outline the 3D contour information of the surrounding environment at 360°
- The farthest measurement distance is up to 200m, and the measurement accuracy is ±3cm
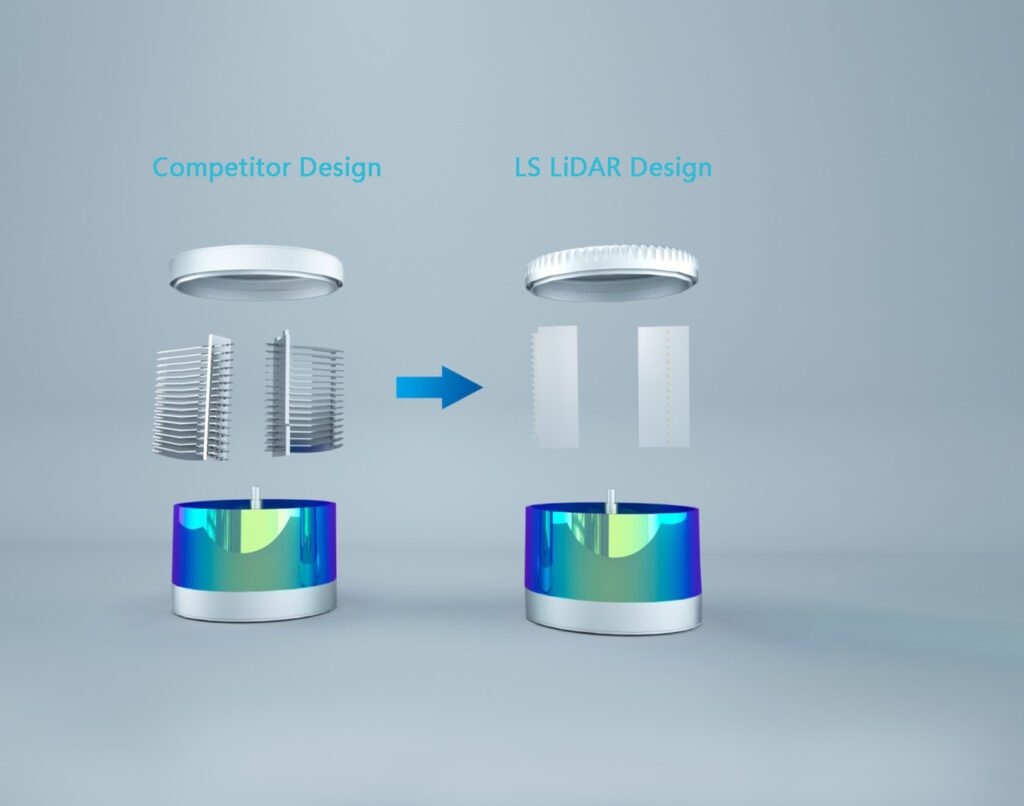
Receiver & Transmitter Highly integrated modular design
- Production assembly – more efficient
- Product performance – more stable
- Product quality – more reliable
Buy Mechanical LiDARs Online
3D Mechanical LiDAR Sensors
-
3D LiDAR Sensors
CX16 3D LiDAR Scanner – 150m – Global Shipping
US$2,187.00 Excl. GST/VAT Add to cartRated 0 out of 5 -
3D LiDAR Sensors
CX32 3D LiDAR Sensor – 150m – DHL Global Shipping
US$3,520.00 Excl. GST/VAT Add to cartRated 0 out of 5 -
3D LiDAR Sensors
C32W LiDAR Scanner – Wide FoV
US$6,660.20 Excl. GST/VAT Add to cartRated 0 out of 5
2D Mechanical LiDAR Sensors
-
Handheld LiDAR Scanner
Trion P1 Handheld LiDAR Scanner
US$8,600.00 Excl. GST/VAT Add to cartRated 0 out of 5 -
2D LiDAR Sensors
N301 2D LiDAR Scanner – Outdoor Use – Global DHL Shipping
US$691.00 – US$746.00 Excl. GST/VAT Select options This product has multiple variants. The options may be chosen on the product pageRated 0 out of 5 -
2D LiDAR Sensors
Anti-Collision LiDAR Scanner – Indoor & Outdoor Use – Global DHL Shipping
US$753.00 – US$829.00 Excl. GST/VAT Select options This product has multiple variants. The options may be chosen on the product pageRated 0 out of 5 -
2D LiDAR Sensors
N401 2D LiDAR Scanner – Outdoor Use – With Reflectivity Data – Global Shipping
US$747.00 – US$802.00 Excl. GST/VAT Select options This product has multiple variants. The options may be chosen on the product pageRated 0 out of 5
Hybrid Solid State LiDAR
Using MEMS technology to drive the rotating prism, the reflected laser beam points in different directions. The advantages of hybrid solid-state lidar include: fast data acquisition speed, high resolution, and strong adaptability to temperature and vibration; through beam control, detection points (point clouds) can be distributed arbitrarily, such as in the distance ahead of the main highway scan , for side scans that are sparse but not completely ignored, with enhanced side scans at intersections. The mechanical lidar, which can only rotate at a constant speed, cannot perform such fine operations.
The following figure shows the working principle of the hybrid solid-state lidar scanners from Leishen CH series hybrid solid state LiDAR:
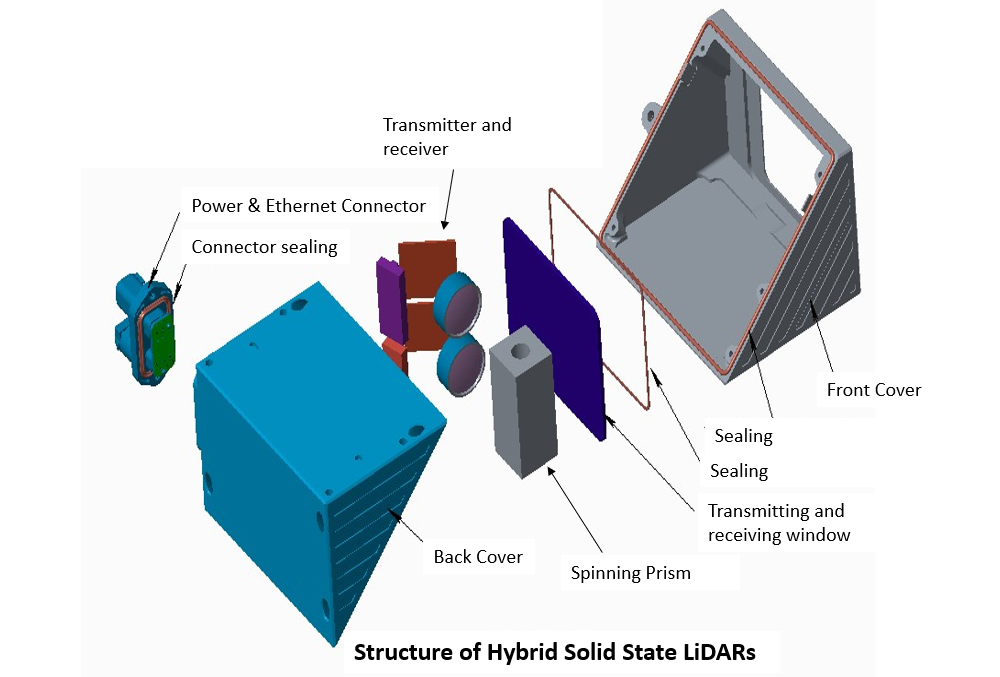
Under the circumstance that the solid-state technology is not mature and ready for commercialize, the hybrid technology is the best solution for harsh working conditions. Comparing to the mechanical lidar scanner, the hybrid solid-state technology doesn’t have the whole electronic structure spinning, but only a spin prism to achieve the scanner while the laser emitter and receiver are static. This design allows the lidar scanner to work under high-vibration condition and achieves long durability, which are the key elements for automotive grade certification.
Buy Hybrid Solid State LiDARs Online
-
3D Hybrid Solid State LiDAR
Automotive Grade LiDAR Scanner – CH32 – Global DHL Shipping
US$2,285.00 Excl. GST/VAT Select options This product has multiple variants. The options may be chosen on the product pageRated 0 out of 5 -
3D Hybrid Solid State LiDAR
Automotive LiDAR Scanner – CH128X1 – Global Shipping
US$4,108.00 Excl. GST/VAT Add to cartRated 0 out of 5 -
3D Hybrid Solid State LiDAR
Wide FoV LiDAR Scanner – CH64W – Global Shipping
US$4,406.00 Excl. GST/VAT Add to cartRated 0 out of 5