Wind Turbine Blade Inspection with Drone Camera - Autonomous flying
get the blades inspected without stopping the turbine - BladeLynx D10 Camera System
powered by Cutting Edge AI Technology
The smartest and most efficient Solution to inspect the wind turble blades with drone - BladeLynx D10 Camera System
Wind turbines are an essential source of renewable energy because they leverage the wind’s power to generate electricity. To maintain optimal performance and safety, periodically inspection of wind turbine blades is a crucial aspect of maintenance. To meet the high standard requirements of market due to high cost of labour, we are bringing AI-powered autonomous drone systems, BladeScan-X10 drone camera system. These systems provide a variety of features that make blade inspections safer, quicker, more effective, and less disruptive to energy production.

High Efficiency
The wind turbine blade inspection efficiency is dramatically improved and cost is significantly reduced. Dynamic inspection can be completed within 15 mins.

Easy & Safe to Operate
Intelligent flight route planning, automonous flying and minimum human interference is required. The wind turbine rotor doesn't need to locked at specific position.

High Precision
Advanced hardware equipment, precise flight routes 100 million pixel camera, millimeter-level defect recognition

Intelligent
Wind turbine attitude analysis, blade defect identification. Automated defect photo analysis and report generation powered by AI
powered by Cutting Edge AI Technology
How BladeLynx D10 Camera system works?
the autonomous drone system for wind turbine blade inspection represents a significant leap forward in renewable energy maintenance. Combining state-of-the-art drones, onboard sensors, and advanced payloads, this system empowers the industry to maintain its assets efficiently, safely, and cost-effectively, ultimately contributing to the sustainable production of clean energy for generations to come.
The system includes:
Drone, remote control, and GNSS base station: by using RTK technology, the drone can be position at centi-meter level accuracy. The drone is also equipped with advanced flight control systems, GPS navigation, and real-time communication capabilities.
Onboard sensors and controller:
Laser Range Finder: The laser range finder is a critical sensor that helps the drone maintain a safe distance from the wind turbine blades and trigger the camera to take the photos when the blade is detected. It ensures that the inspection process is carried out with precision and safety in mind.
Drone-Based Controller: This controller is the brain behind the drone’s autonomous flight. It processes data from various sensors, executes flight plans, and ensures that the drone follows the predetermined inspection route accurately. It also incorporates obstacle avoidance algorithms to guarantee safe navigation;
Payloads:
Cameras: High-resolution cameras capture detailed images of the wind turbine blades. These images provide essential visual data for assessing the condition of the blades, detecting defects, and identifying areas in need of maintenance or repair.
LiDAR (Light Detection and Ranging): LiDAR sensors play a crucial role in creating 3D models of the wind turbine and its surroundings. By emitting laser pulses and measuring their return times, LiDAR sensors generate precise, detailed maps that facilitate accurate assessments of the turbine’s condition.
Work station:
The work station is used for wind farm and wind turbine information management. It is also the processer for flight planning during static inspection, and the embeded AI algorithm can also analyze the images captured and generate the reports.
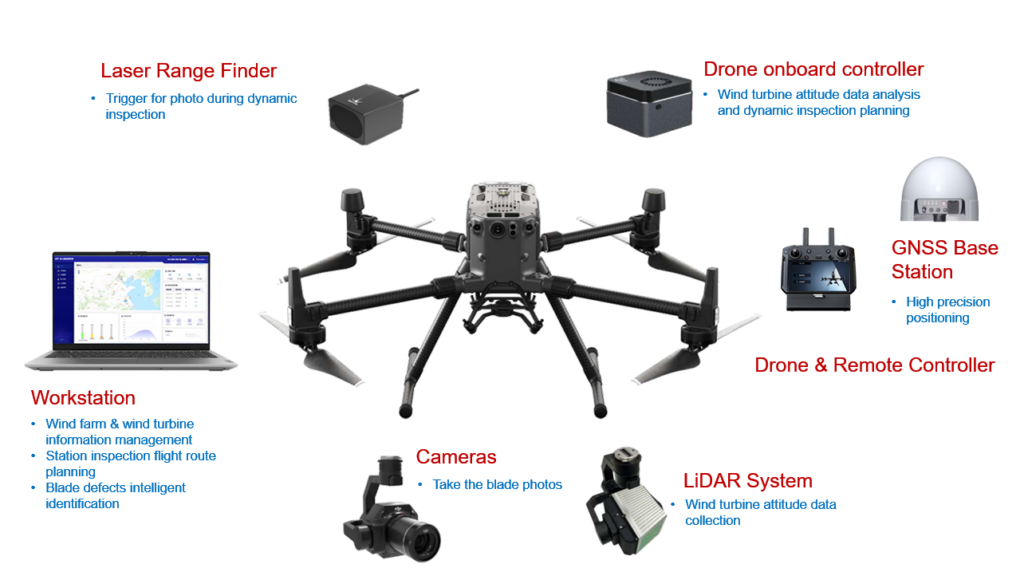
powered by Cutting Edge AI Technology
key Features of BladeLynx D10 Camera Dynamic Blade Inspection Solutions
We can inspect wind turbine blades with our autonomous drone system in both static and dynamic methods:
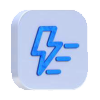
Dynamic Blade Inspection - Turbine stop & Rotor lock are not required
Inspection condition:
- No need to stop the wind turbine;
- Rotor speed requirements: 5rpm – 10rpm
- Wind speed requirements: less than 8m/s;
Inspection Duration:
15 mins
Defects dimensions
Centi-meter level
Items can be inspected:
- Pressure side/suction side housing
- Blade tip & root
- leading edge/trailing edge
- hub
- nacelle and top accessories
- Tower inspection routes can be added as needed
Blade defect classifications - Powered by AI
Defect type | Coding/Algorithm Category | Defect description | Degree/size | Defect level | Handling suggestions |
---|---|---|---|---|---|
Parts missing | DS | Lightning arrester is missing | full quantity | 1 | Periodic inspection/repair |
Rain cover dislocates/falls off | full quantity | 1 | Periodic inspection/repair | ||
Blade power enhancement component is damaged/lost | full quantity | 1 | Periodic inspection/repair | ||
surface contamination | WR | Surface dust, oil, dead insects, tape | Full Size | 1 | Periodic inspection/repair |
surface corrosion | FS | Bubbles, blisters, thickness waves | Full Size | 1 | Periodic inspection/repair |
touch up paint | BQ | Touch up paint traces | Full Size | 1 | Periodic inspection/repair |
peeling paint | DQ | The surface finish is peeled off/scratched/damaged/peeled (the fiberglass layer is not exposed) | Full Size | 1 | Periodic inspection/repair |
The front edge protective paint peels off (the fiberglass layer is not exposed) | Full Size | 1 | Periodic inspection/repair | ||
Gel coat peeling off | TL | A small area of gelcoat is peeled off/damaged (the fiberglass layer is exposed but not damaged) | S≤100c㎡ | 1 | Periodic inspection/repair |
Large areas of gelcoat peeling off/damaged (the fiberglass layer is exposed but not damaged) | S>100c㎡ | 2 | Periodic inspection/repair | ||
small area of leading edge gel coat is corroded and peeled off (the fiberglass layer is exposed but not damaged) | L≤10cm | 1 | Periodic inspection/repair | ||
A large area of front edge gelcoat is corroded and peeled off (the fiberglass layer is exposed but not damaged) | L>10cm | 2 | Periodic inspection/repair | ||
Fiberglass corrosion | BX | Corrosion of small area fiberglass layer | S≤100c㎡ | 2 | Periodic inspection/repair |
Corrosion/cracking of fiberglass layer on small size leading edge | L≤10cm | 2 | Periodic inspection/repair | ||
Large area of fiberglass layer surface damaged | 100c㎡3 | Limited power operation, fault shutdown/repair |
| ||
Corrosion/cracking of large front edge fiberglass layer | 10cm3 | Limited power operation, fault shutdown/repair |
| ||
Extremely large area of fiberglass damage | S>500c㎡ | 4 | Emergency shutdown/repair, replacement | ||
Oversized leading edge fiberglass corrosion/cracking | L>50cm | 4 | Emergency shutdown/repair, replacement | ||
Cracked front and rear edges | KL | Small size front and rear edge cracks | L≤10cm | 2 | |
Large front and rear edge cracks | 10cm3 | Limited power operation, fault shutdown/repair |
| ||
Super large-scale front and rear edge cracks | L>50cm | 4 | Emergency shutdown/repair, replacement | ||
drumming | QG | The surface of the small area of glass fiber layer is bulging and delaminating. | S≤500c㎡ | 3 | Limited power operation, fault shutdown/repair |
Large area of glass fiber/core material bulging and delamination | S>500c㎡ | 4 | Emergency shutdown/repair, replacement | ||
crack | LW | Transverse cracks on the surface of small-sized shells | L≤50cm | 3 | Limited power operation, fault shutdown/repair |
Longitudinal cracks on the surface of small-sized shells | L≤100cm | 3 | Limited power operation, fault shutdown/repair | ||
Transverse cracks in main beam | L>1cm | 4 | Emergency shutdown/repair, replacement | ||
Root transverse cracks | L>1cm | 4 | Emergency shutdown/repair, replacement | ||
Bilateral penetrating transverse cracks | Full Size | 4 | Emergency shutdown/repair, replacement | ||
Longitudinal cracks on the surface of large shell | L>100cm | 4 | Emergency shutdown/repair, replacement | ||
Broken blade tip | YJPS | Blade tip damage/casing missing | S≤500c㎡ | 3 | Limited power operation, fault shutdown/repair |
Small size aluminum tip edge cracking | L≤20cm | 3 | Limited power operation, fault shutdown/repair | ||
Aluminum tips fall off and edges of large aluminum tips crack | L>20cm | 4 | Emergency shutdown/repair, replacement | ||
lightning strike | LJ | Small yellow/black burn area | L<30mm | 2 | Periodic inspection/repair |
Large yellow/black burn area | L>30mm | 3 | Shutdown/Repair: Polish the coating to the main body and repair the coating; observe the damage to the main body after polishing to the main body | ||
ice covering | FB | Blade surface covered with ice | 3 | Limited power operation, fault shutdown/repair | |
Fracture (structural damage) | SH | Main beam fracture | L>1cm | 4 | Emergency shutdown/repair, replacement |
Large area of shell torn | S>500c㎡ | 4 | Emergency shutdown/repair, replacement |
Photo Examples
Photo examples are shown below (not the full set), and, they are also compressed during upload to the website.
Please proceed to GoogleDrive via the link below to download original quality photo below:
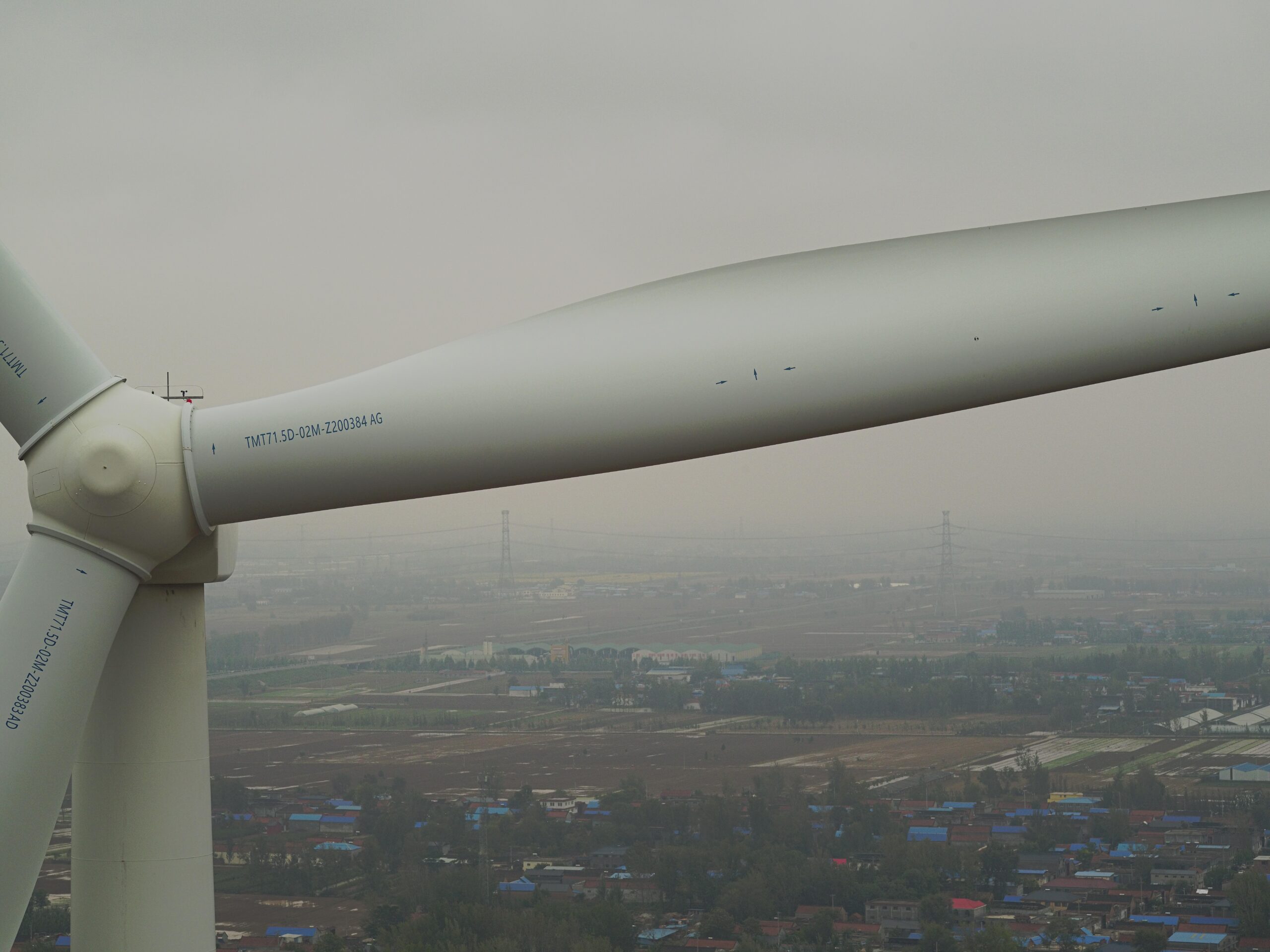
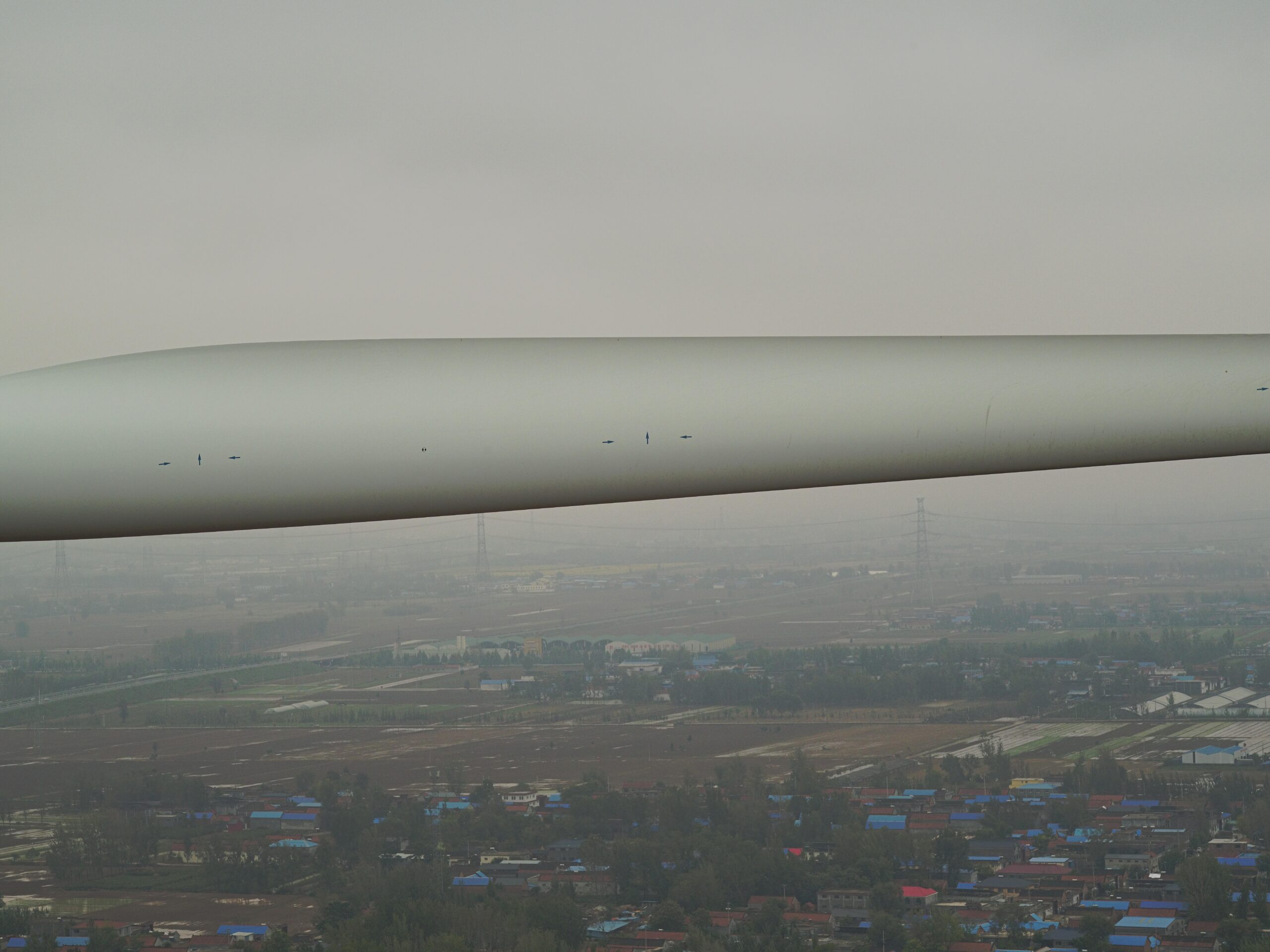
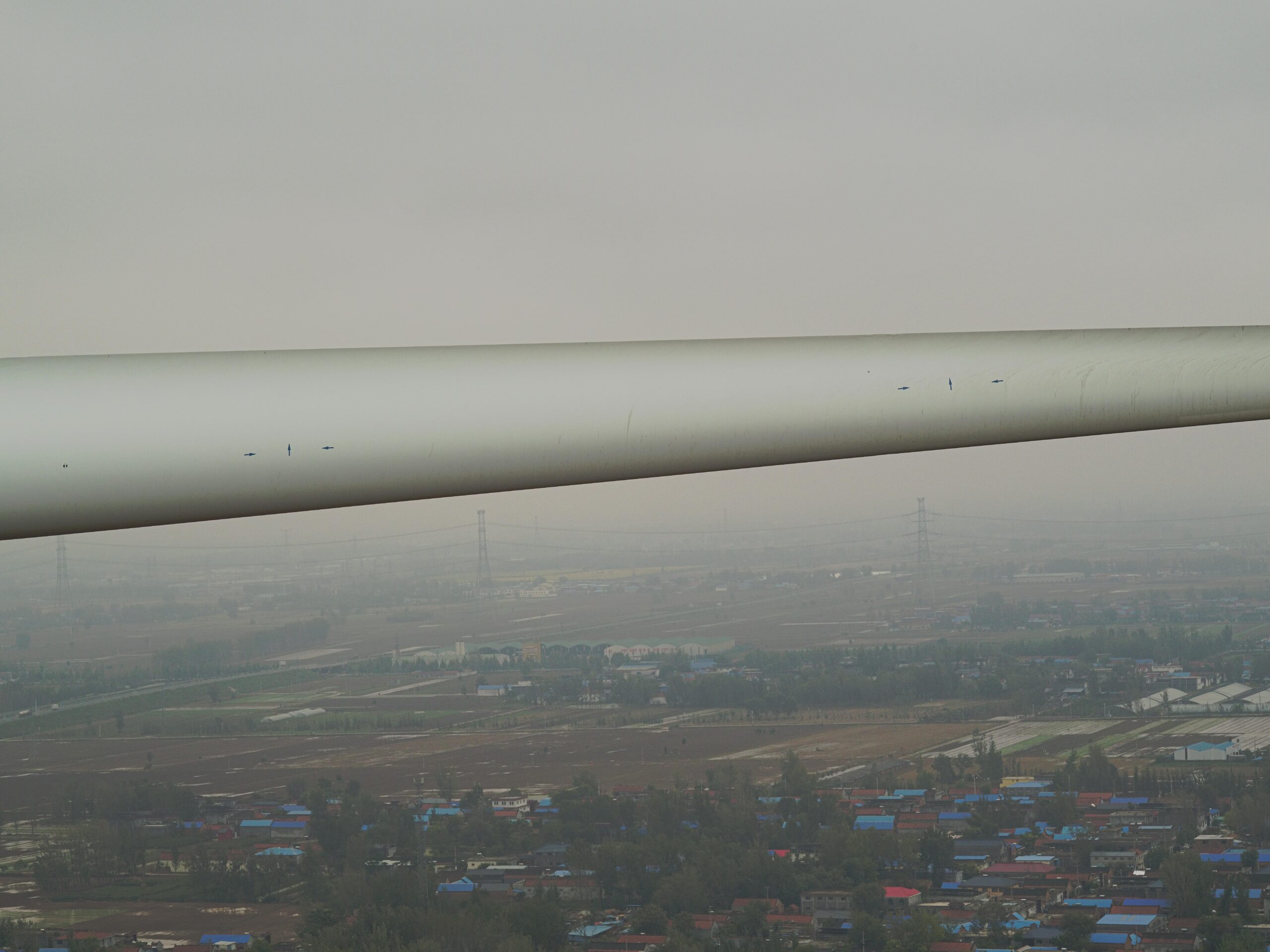
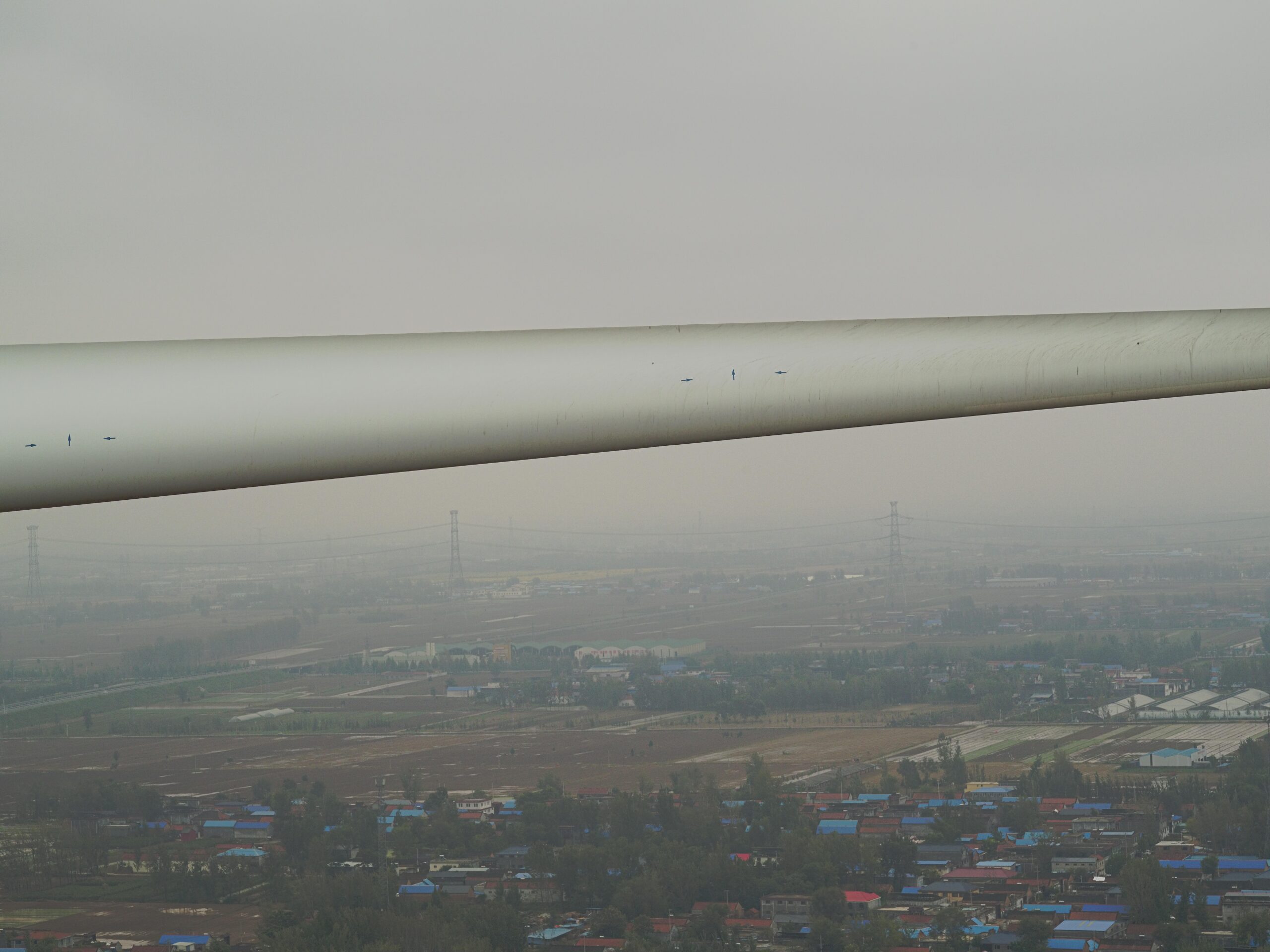
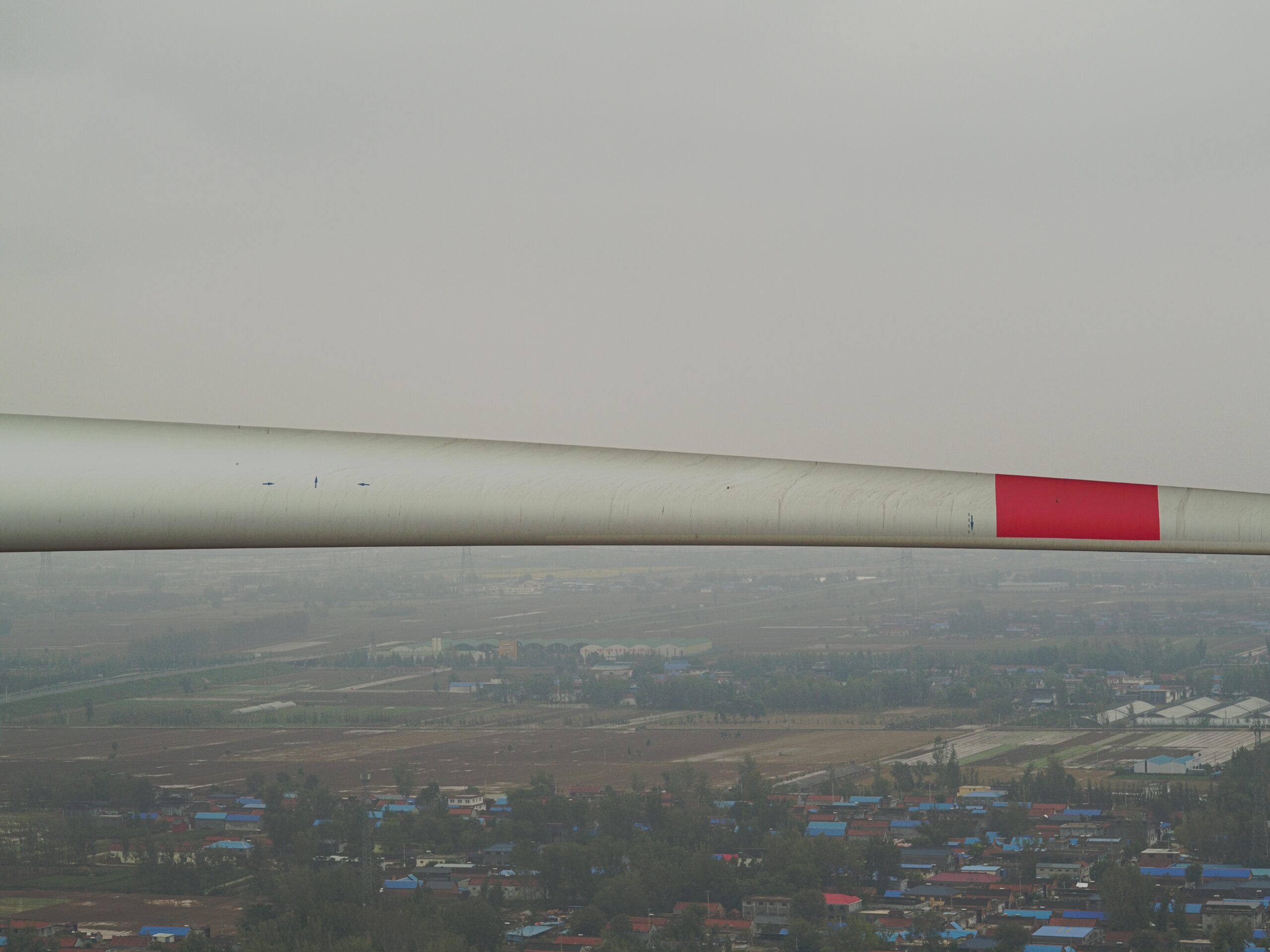
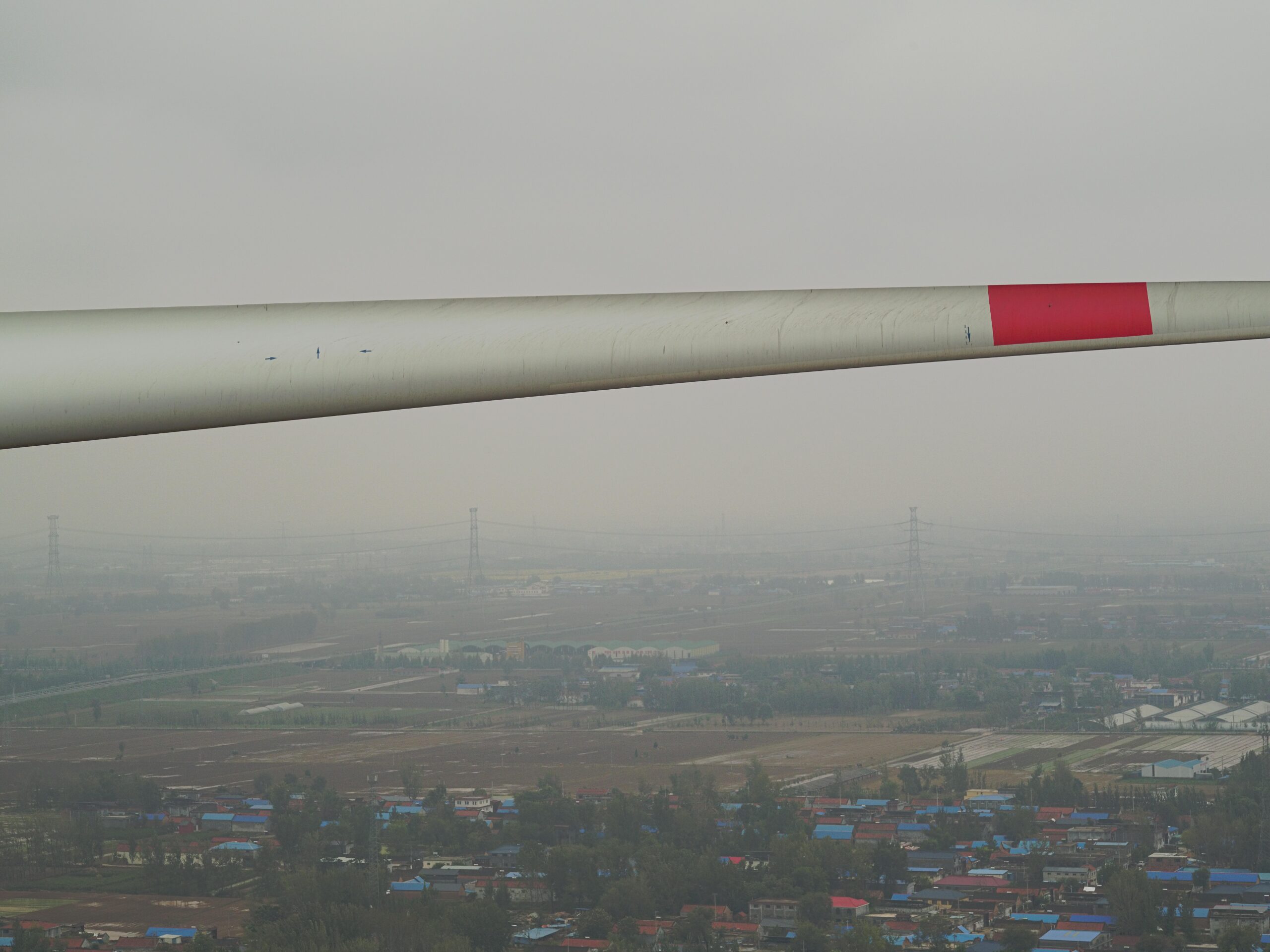
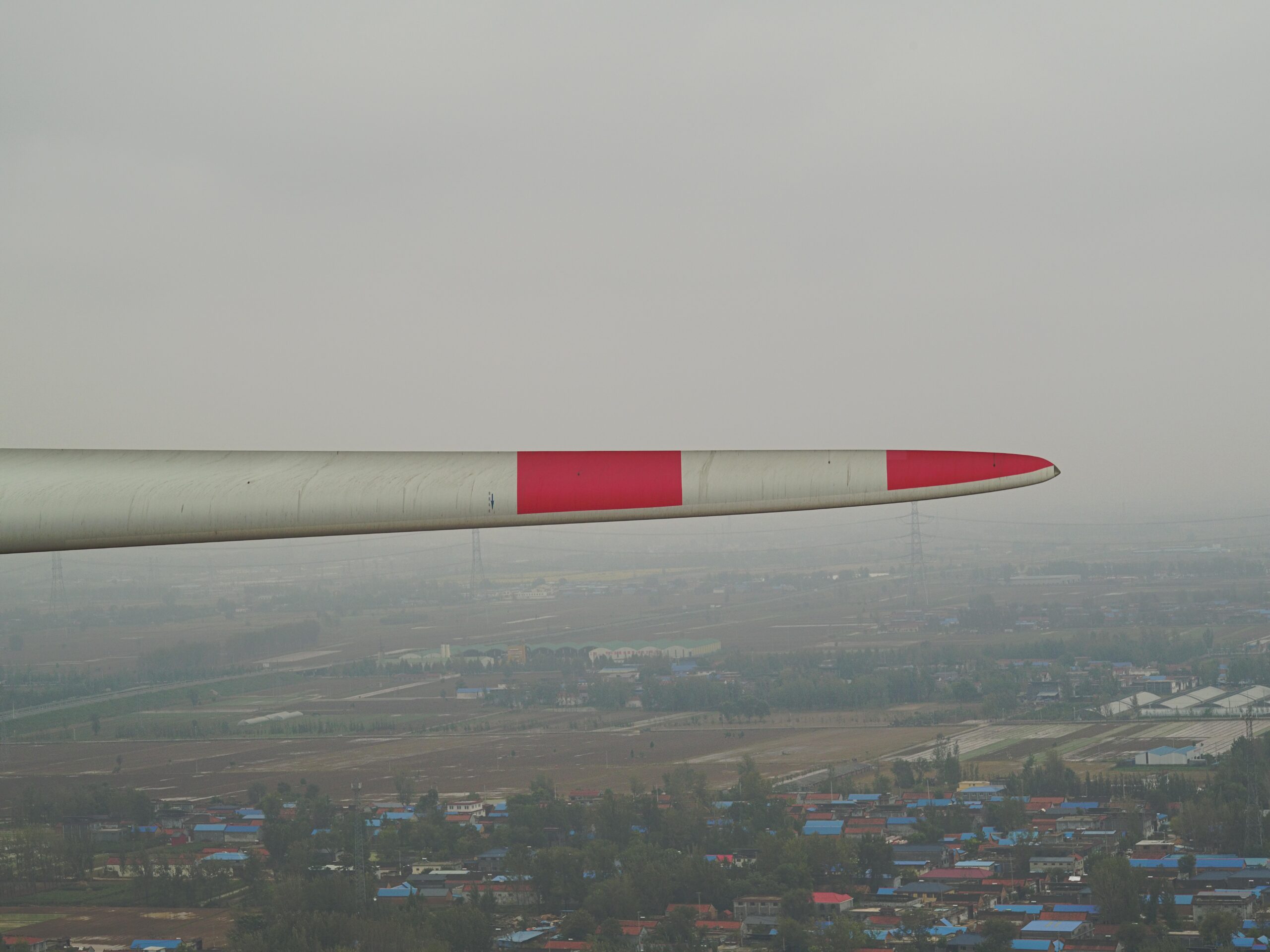
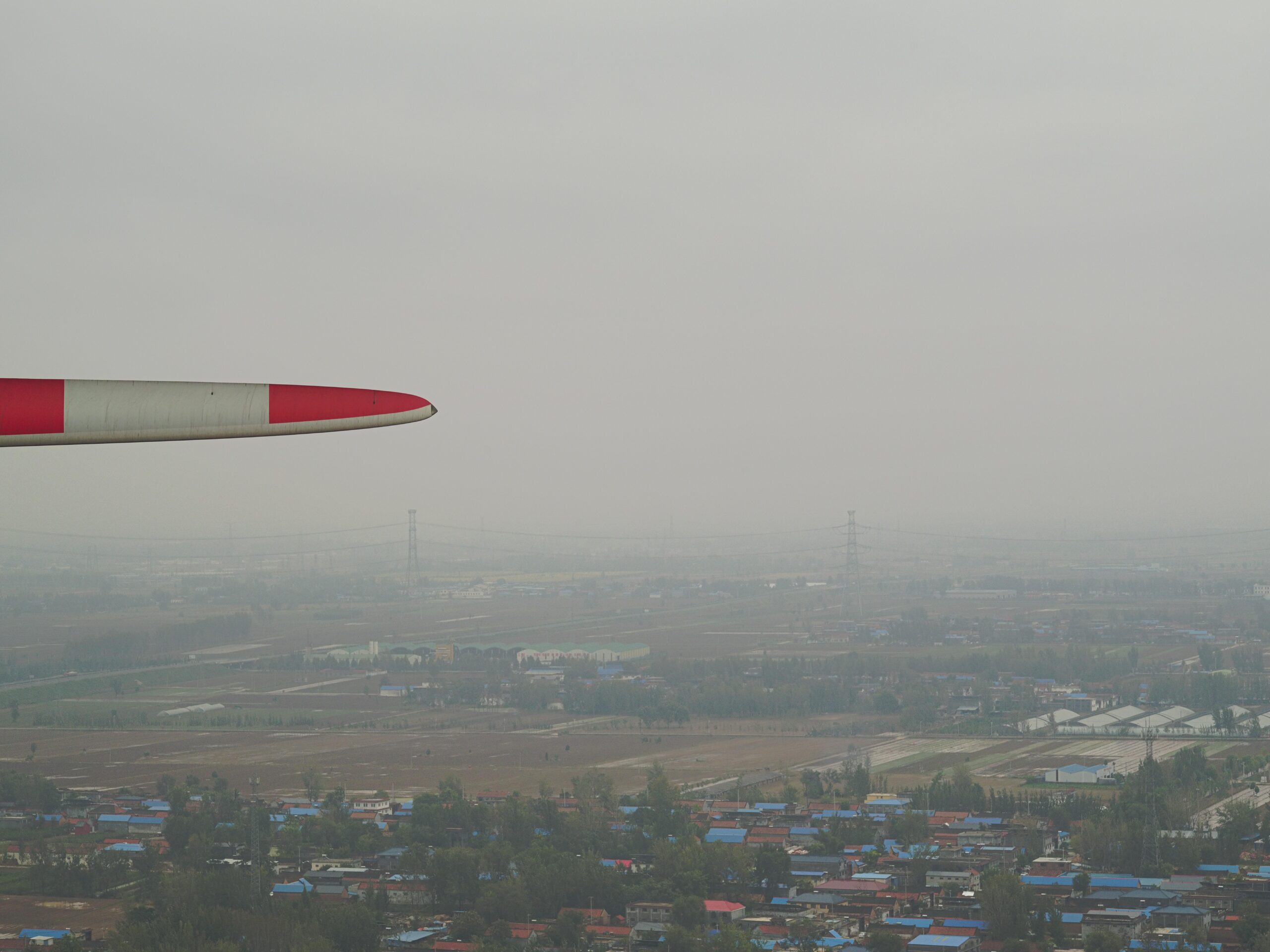
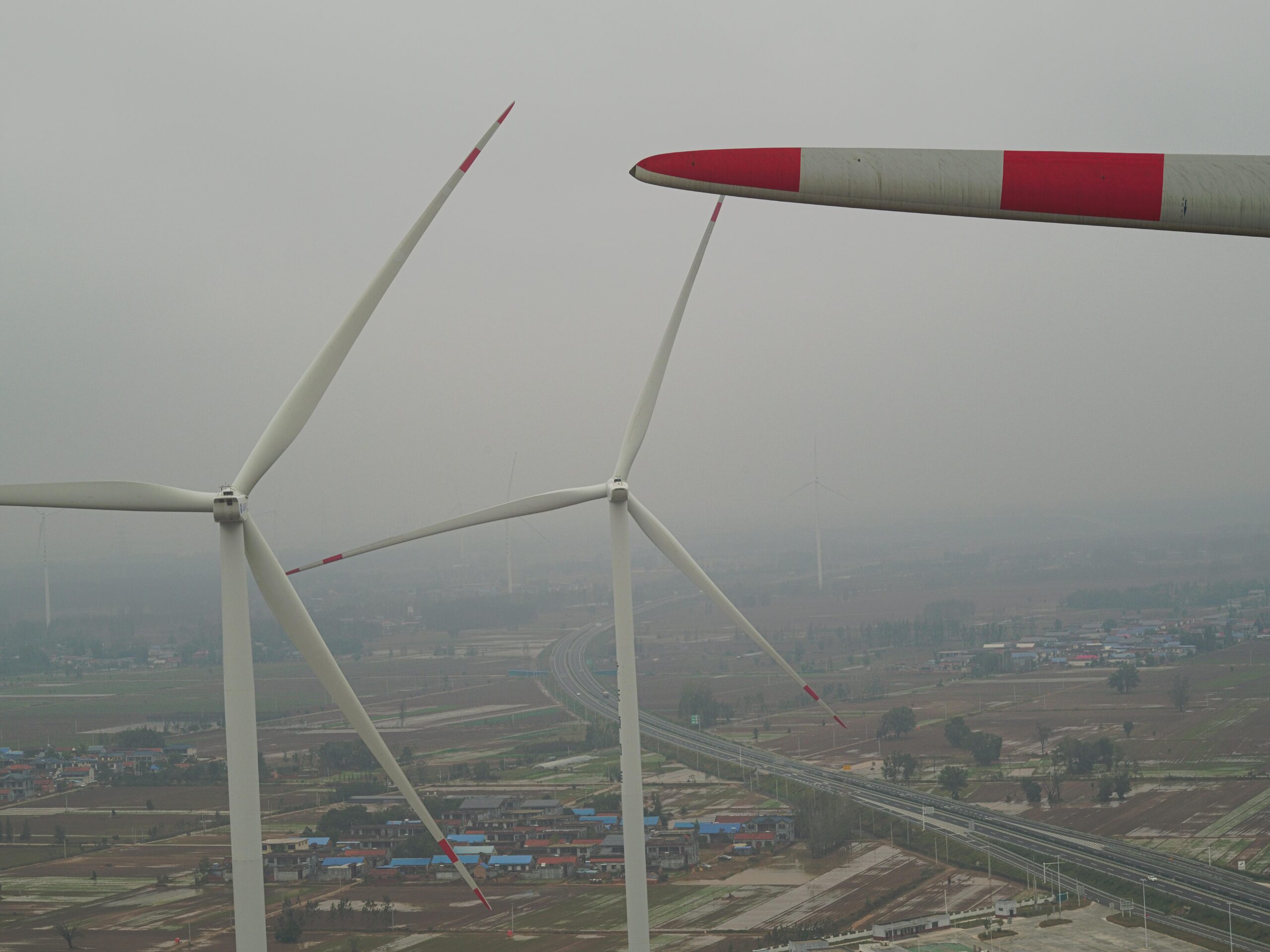
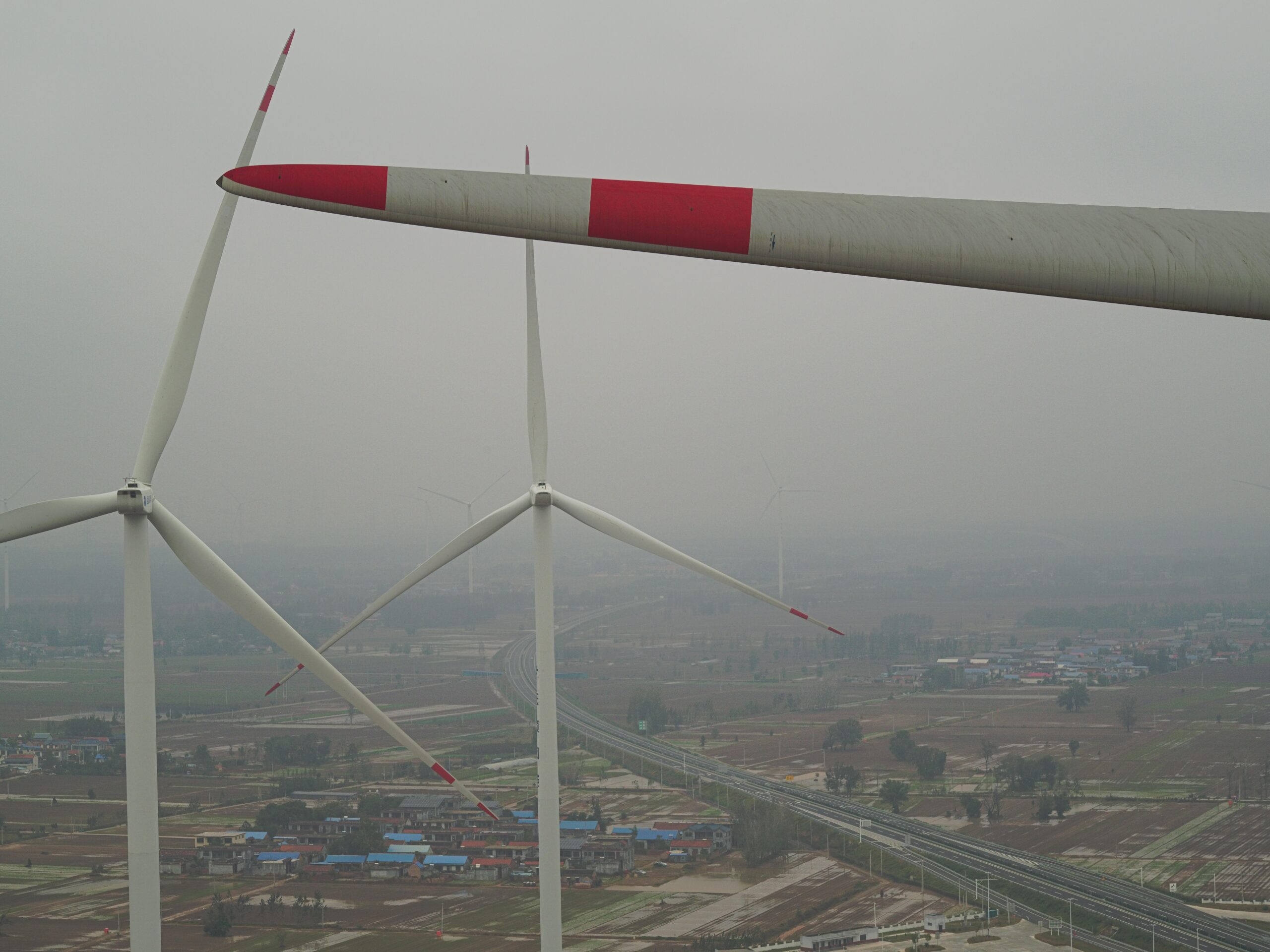
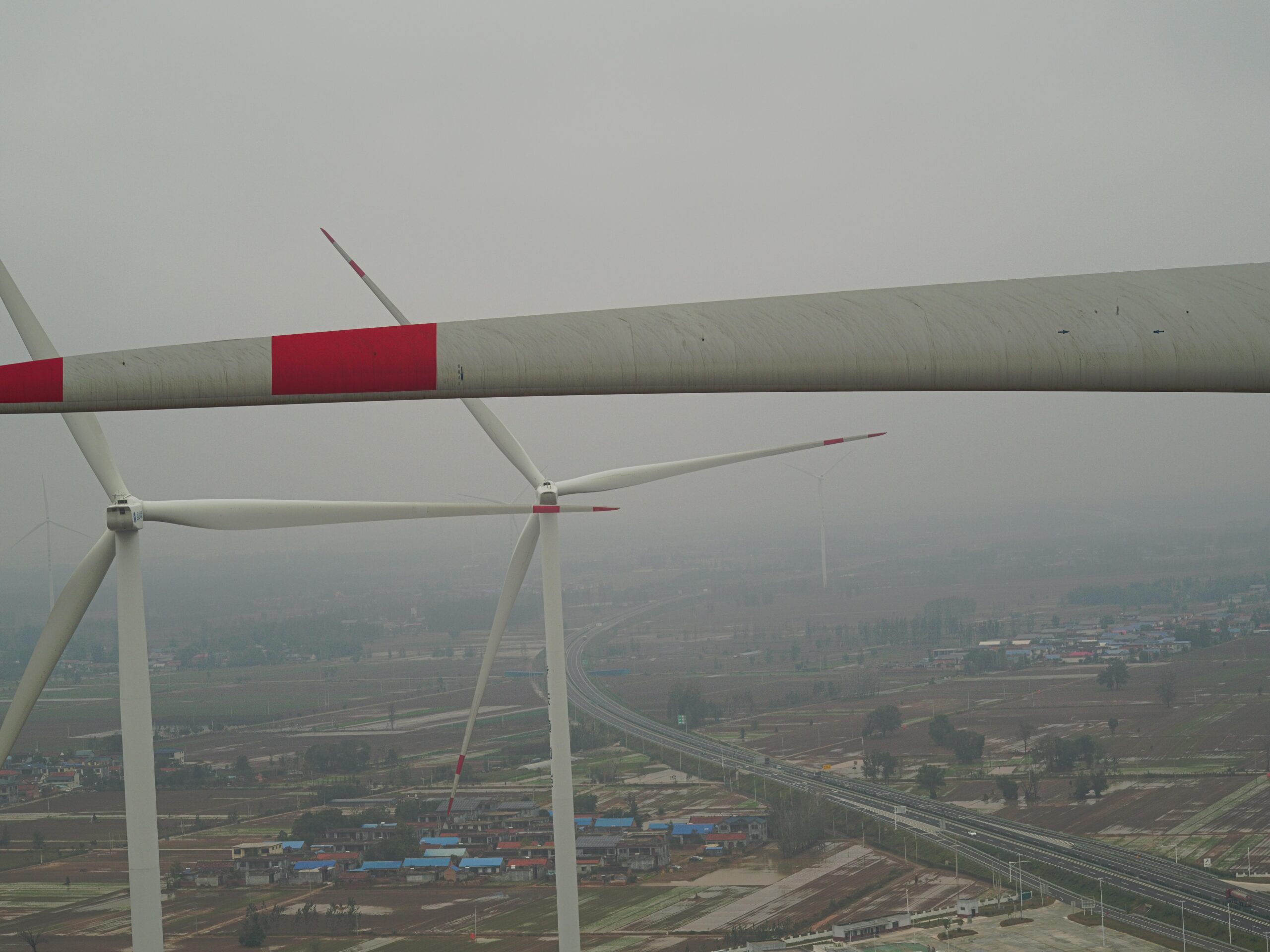
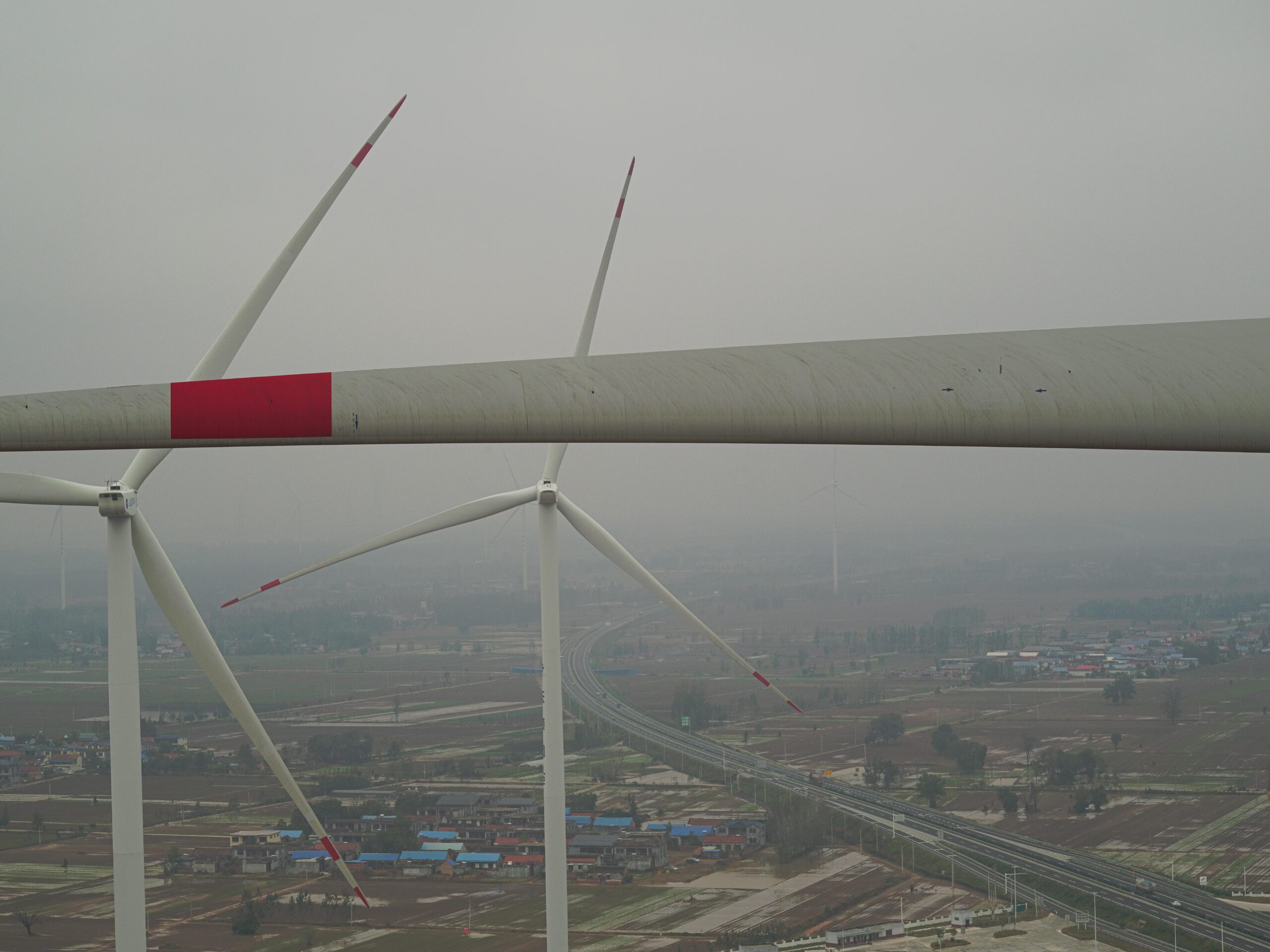
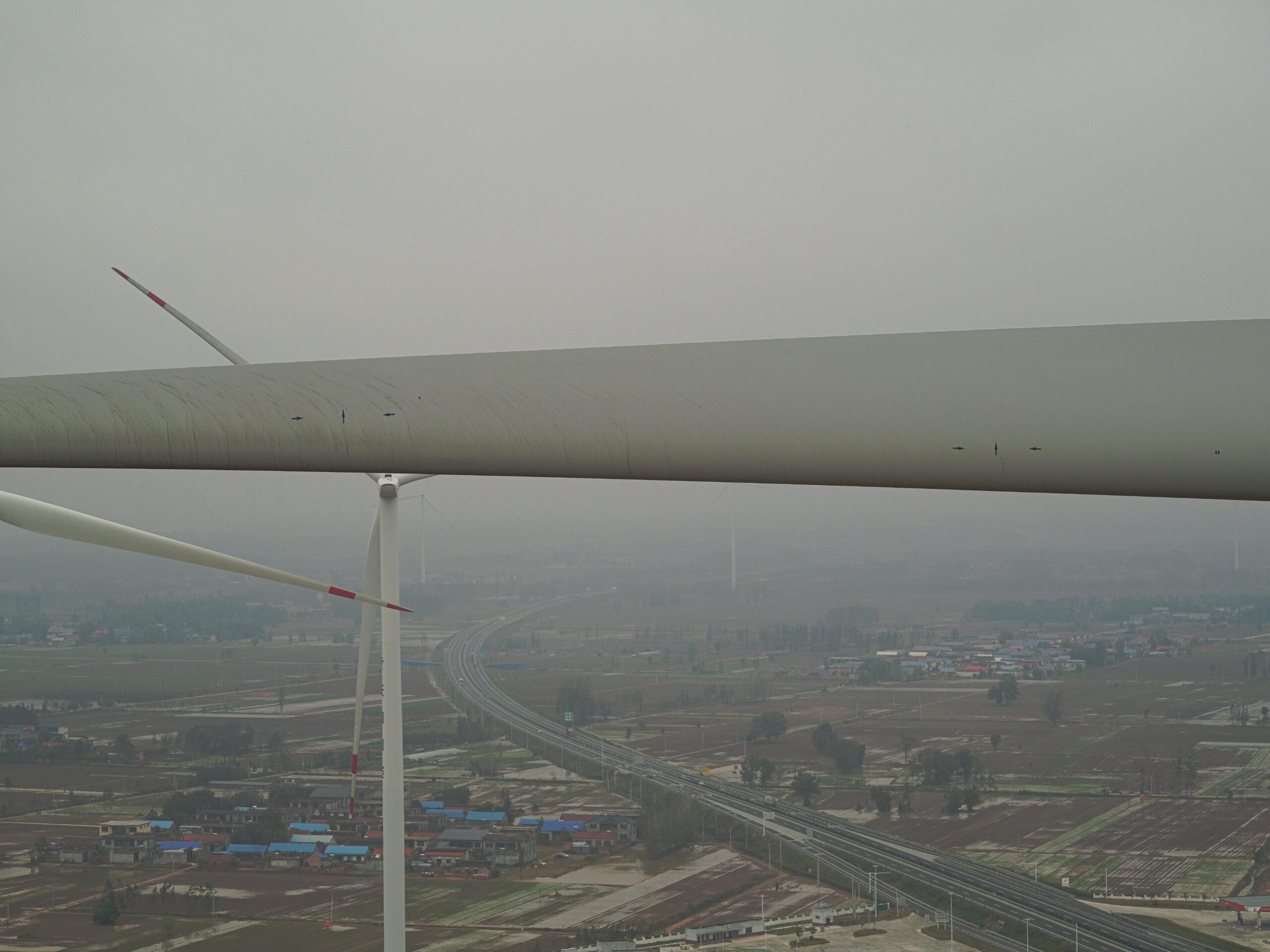
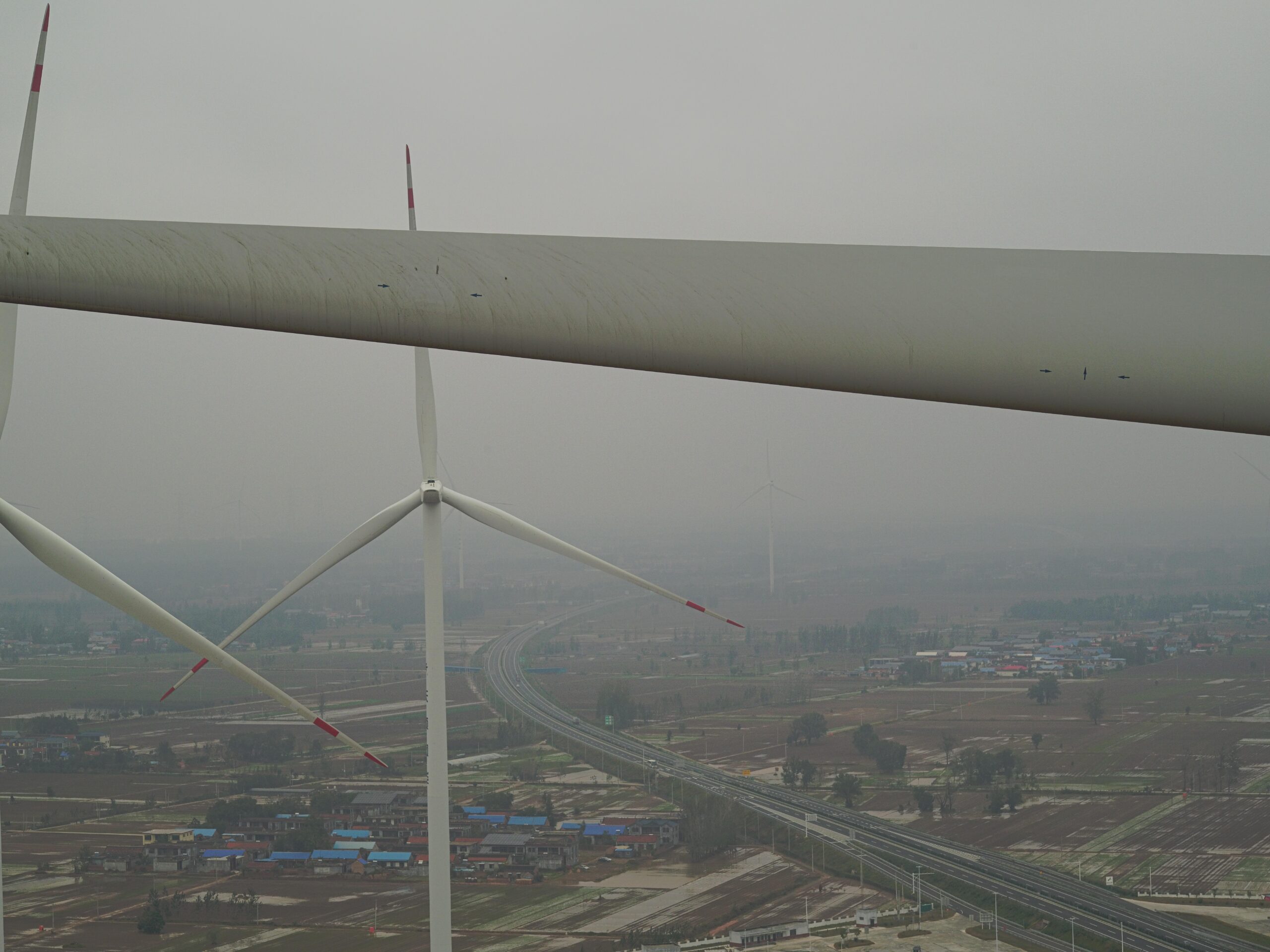
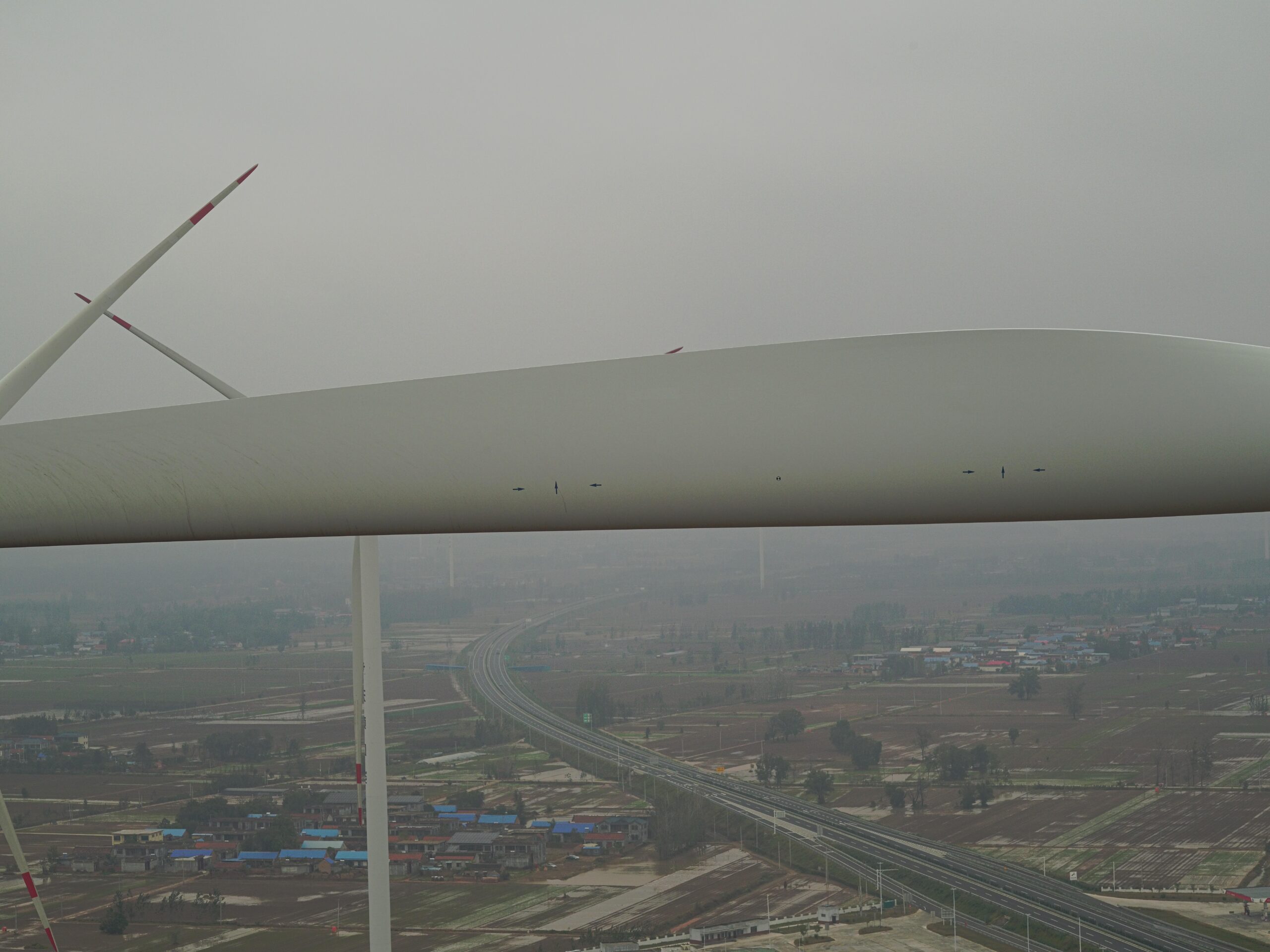
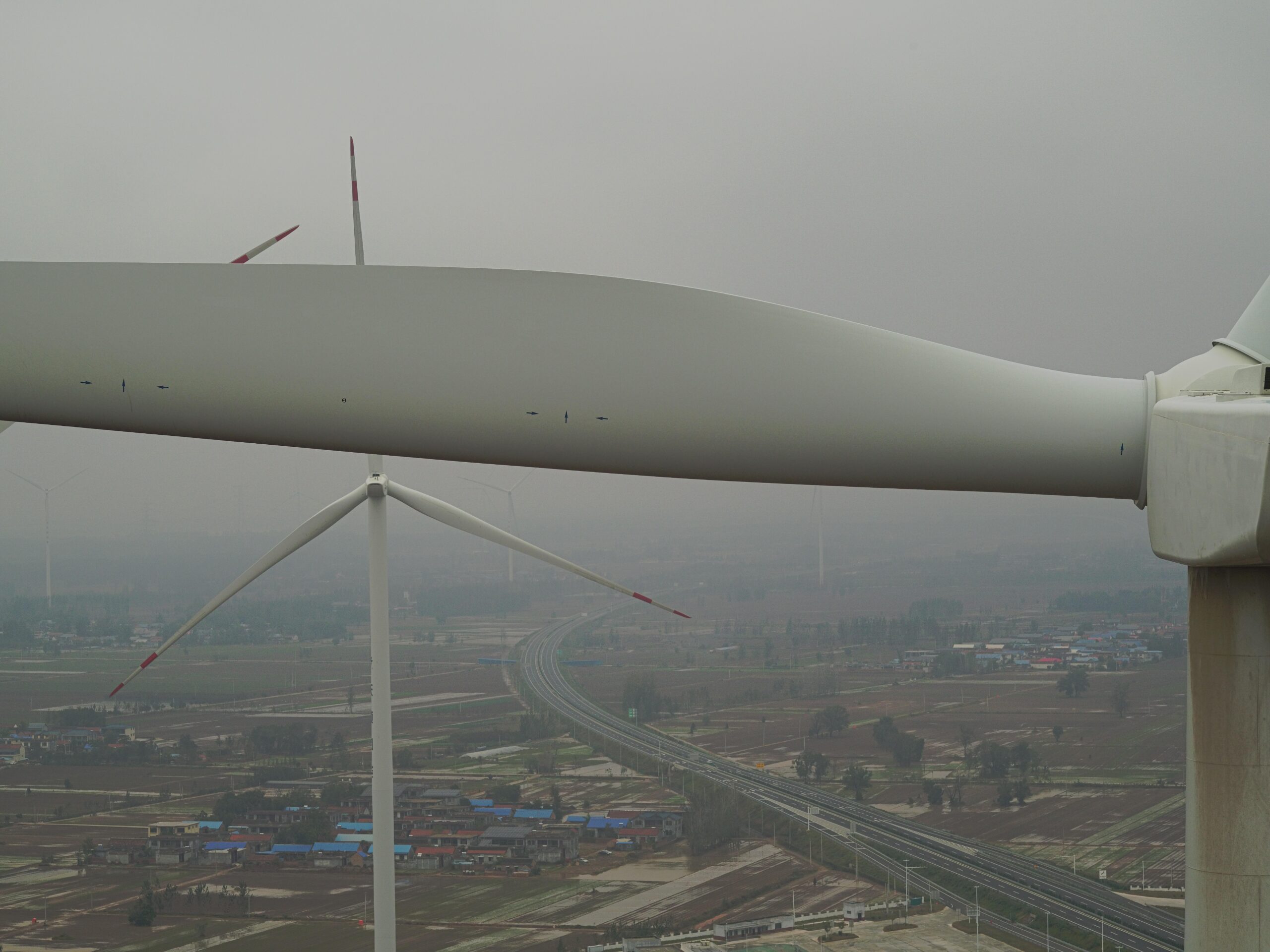